CATL’s Sichuan plant selected as Lighthouse factory by World Economic Forum
NINGDE, China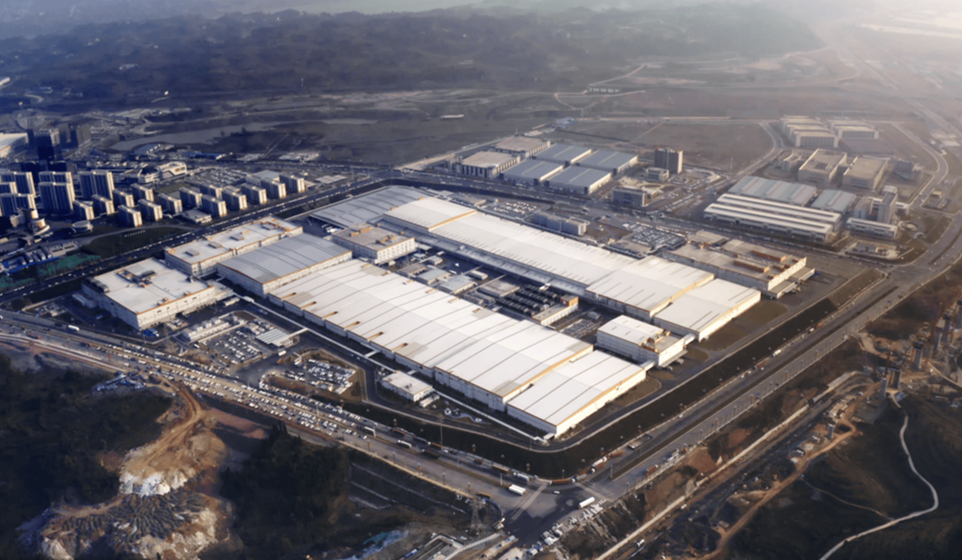
Sichuan Contemporary Amperex Technology Limited (CATL-SC), a wholly-owned subsidiary of CATL, has been added to the Global Lighthouse Network (GLN) by the World Economic Forum, making it CATL’s second Lighthouse plant following its Ningde facility, which was included in GLN in 2021. So far there are only two Lighthouse factories in the battery industry globally, both of which are CATL’s production facilities.
The World Economic Forum made the following remarks about CATL: “To catch up with significant business growth, and higher quality and sustainability expectation, CATL builds up a large greenfield in Yibin city. The plant further deployed in depth AI, IoT and flexible automation on top of CATL Ningde headquarters lighthouse digital initiatives, and has achieved 17% increased line speed, 14% reduced yield loss, and zero carbon emission.”
The Global Lighthouse Network is a community of manufacturing sites that show leadership in the adoption and integration of the cutting-edge technologies of the Fourth Industrial Revolution. Francisco Betti, Head of Advanced Manufacturing and Value Chains at the World Economic Forum, said: “The new factories of the Global Lighthouse Network show how manufacturers can meet business goals while having a positive impact on economies, peoples’ livelihoods and the environment. The challenge for companies and policymakers is how much they can scale-up these innovations across whole production networks and value chains.”
Fourth Industrial Revolution technologies drives productivity, sustainability and resilience
In the context of comprehensive digital transformation of battery industry, CATL is accelerating digital innovation in battery’s full life cycle regarding battery design, manufacturing, utilization, and recycling, so as to meet the requirements for high precision process, fast production speed, and high quality.
– Green Energy Management. CATL has developed an energy management system that collects data from over 40,000 sensors deployed in the plant through Narrow Band-IoT & 5G wireless solutions. Supported by an advanced algorithm, the system has calculated each equipment’s operating parameters with optimized energy consumption of the system.
– Intelligent production management. By developing a closed-loop coating process control algorithm, CATL-SC is able to model and deeply learn the combined parameters of more than 1,000 powders and fluids, achieving precise control of foil coating in micron and milligram levels, thus greatly improving the consistency of products.
Also, based on virtual and simulation development, pack lines of CATL-SC have achieved 80% automatic. Supported by automatic gluing process, the manpower of the gluing process line is reduced by 70%, achieving 99.8% qualified rate.
– Extreme quality management. With the application of high-precision visual inspection equipment and AI technology, CATL-SC has achieved recognition accuracy to micron level, which stimulated breakthroughs of defect detection in process of welding, winding and previous process under high-speed fluid condition.
– Highly precise safety management. Safety management is crucial to CATL-SC, which is currently one of the largest EV battery production bases in the world. By combining video streaming and AI technology, it has reduced the risk of missed inspection. Through video streaming, the system can automatically identify operation mistakes such as mixed placement of signs and channel occupation, and is able to label and save images automatically. Supported by infrared thermal and AI technology, it has centralized temperature monitoring of battery cells in warehouses and temperature monitoring of battery cells in key high-temperature processes.
As a global leader to achieve the world’s first Lighthouse factory in the battery industry, CATL has reduced the defect rate of its products to PPB level. It is now in an effort to replicate its Sichuan plant’s experiences in agile and flexible intelligent manufacturing in all its 13 production bases worldwide, thus contributing to the high-quality development of the new energy industry amid the Fourth Industrial Revolution.
SOURCE: Contemporary Amperex Technology Co., Limited